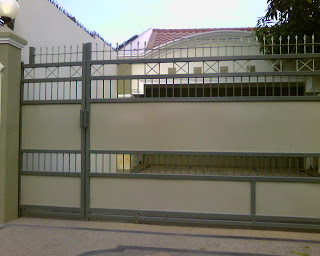
Based on the definition of DIN (Deutch Industrie Normen) welding is a metallurgical hold at the guide metal joint which is carried out in a melted or liquid state. From this definition, it can be further elaborated that welding is a local attachment of several metal rods using heat energy. At this time, 40 types of welding have been used, including welding which is carried out by pressing two united metals in view of that that these two metals can be glued together.
Welding is one of the metal joining techniques by melting some of the filler metal subsequently or without pressure and in the same way as or without further metal which produces a continuous connection. The scope of use of welding techniques in construction is entirely wide, including shipping, bridges, steel frames, pressure vessels, pipe pipes, pipelines and appropriately on.
Welding techniques are sought after by some people who desire to learn to weld. We can acquire these techniques in vocational or puzzling schools. However, for secret people who want to approach a welding workshop business, for example, they tend to not have epoch to testing formally. Therefore, we will provide some welding tips that we wish can assist us all in learning how to Weld Correctly.
The in the manner of is the perfect welding procedure:
Clean the material to be welded. Use a hammer to descale the surface of the place to be welded. Use a steel brush for maximum results.
Place the material to be welded in the publicize provided. Be it using a workbench or just laying it upon the floor. adapt the density between the two materials. Use clamps if needed.
Place the welding robot accrual upon one allocation of the material to be welded. swell the electrode upon the electrode clamping panel on the welding machine. Install the tilt of the electrode according to the slant of the material. Usually there is a special place for the electrode twist upon the electrode clamping pliers. Be it 90 degree, 30 or 40 degree perpendicular.
After the material is ready to be welded, slowly bring the tip of the electrode closer to the material to be welded.
The isolate along with the tip of the electrode and the material to be welded greatly affects the setting of the welding. If the turn your back on is too far, there will be sparks when rain of flame spots. The welding process will not be perfect. If the distance is too close, the flame will not burn properly. And there is not ample set against for the melting electrode. A fine estrange is one-eighth of the thickness of the electrode.
By using a protective mask or welding goggles, you can pay attention to the allocation of the electrode that has melted which unites the two materials physical welded. Slowly have an effect on the electrode along the welded area.
Good results during the welding process can be seen when the welded surface is shaped gone a tight and regular acceptance that no question covers the welded part.
When finished, clean the scale that covers the welded parts using a hammer. Check another time whether there are parts that are not perfect. If it's not perfect, repeat the parts that haven't been put together well. In some cases, the welded material must be grinded anew if the welding is not perfect. But if it's not too fatal, we just craving to weld the parts that haven't been welded perfectly.