HSS drills are an economical option for low-volume gap manufacturing.
- By Lindsay Luminoso
April 29, 2019
Article
Cutting Tools
Join Discussion
The HX Jobber drill series combines the strength of HSS with a 135-diploma break up point to allow lower thrust requirements, improved slicing action, and reduced walking. Photo courtesy of Dormer Pramet.
Carbide drills have substantially taken over high-pace steel (HSS) drills within the business. Before 2000 the market split between carbide and HSS drills was at about 50-50. The market share for HSS slowly shrank and at this time it sits roughly at 10 to 15 per cent of all drill purchases. However, millions of holes still are being made with HSS drills.
Characteristics
"HSS drills have increased toughness and lower hardness when in comparison with their carbide counterparts," mentioned Adam Dimitroff, utility engineer, OSG Canada.
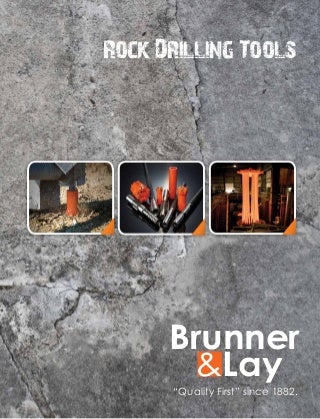
Under certain conditions, particularly when the operator with a hand drill begins to suffer fatigue, a carbide choice has the potential to interrupt, whereas the HSS option will stand up better to that flex.
"The power to flex has becomes an enormous benefit in unstable conditions-older machines with poor spindle runouts, loose slideways or fixtures, and in lots of other conditions," stated Sarang Garud, product manager, marketing, Walter USA LLC.
When HSS drills were first coming into the market, they often came with a chisel level. The centre of the drill didn’t flip very quick however pushed and extruded the fabric till the lips could come and lower it.
"Today’s HSS drills have been configured to incorporate cut up points which can be able to grab the material and enter rapidly, making accurate holemaking easier," mentioned Dan Cormier, regional sales manager, Dormer Pramet.
Typically, HSS drills have a 118-diploma angle on the drill point, though in recent years many manufacturers have introduced drills with 135-degree and 140-degree angles. A 135-diploma drill is flatter than a 118-diploma option, allowing the cutting lips to engage with the fabric sooner and start full metallic reducing action quickly. However, the 118-diploma option stays the usual configuration.
These traits assist improve device life as HSS drills are inclined to spend much less time in the minimize due to their material softness.
Applications
HSS drills generally are present in machine shops with low-quantity runs through which some holes are being drilled but not too many per shift. They're additionally fitted to shops the place the equipment’s cutting speeds are restricted, functions with heavy interruptions, and weak setups. In these situations, HSS drills show to be an economical possibility.
"These drills are appropriate for non-ferrous supplies because they typically have a sharp edge," said Dimitroff, "Whereas carbide drills typically have a honed edge to combat the brittleness of carbide material. Non-ferrous metals are also very delicate and do not trigger instruments to wear as a lot as steel alloys. They are additionally appropriate for interrupted cuts attributable to their higher toughness."
The Walter Titex A1249XPL HSS drill’s wider flute design allows for higher chip evacuation and helps with flood (exterior) coolant in addition to pecking. Photo courtesy of Walter USA.
Our specialists agreed that when a machine doesn't have internal coolant capabilities, HSS drills are the primary selection for drilling stainless steel supplies.
In response to Garud, if the machine doesn’t have a coolant-by means of option, these drills can be used with the pecking cycle. The general process is sluggish, however this allows the machine for use. If you have any thoughts regarding in which and how to use drills supply, you can get in touch with us at the web-page. He added that some retailers also go for HSS drills when producing holes in costly elements.
"If the HSS drill breaks contained in the part, it may be drilled out," mentioned Garud. "If a carbide drill breaks inside an expensive half, it may be very arduous to take away. Also, smaller retailers have always preferred HSS for price if not performance. Particularly with small and medium collection production, with unstable machining conditions and all the time when toughness is required, customers continue to rely on drilling tools in excessive- speed steel."
Cormier stated that HSS drills are additionally used in hand drilling functions, which are numerous. Millions upon hundreds of thousands of holes are drilled by hand. He offers the examples of aircraft skins and upkeep, restore, and overhaul (MRO). Using a HSS drill with split points permits fast entry into the material with no strolling. If the drill desires to walk or move to the aspect, the opening won’t start in the right position, which may very well be extraordinarily detrimental in precision positions on an aircraft. When a gap is being drilled to hold the skin on the wing or fuselage, you actually need it in its precise location.
The consultants said that HSS drills are generally used within the aerospace industry the place deep reach however shallow hole depth is needed. Cormier added that drilling is a multimillion-dollar enterprise in Canada’s aerospace business with players like Bombardier, MHI, IMP, KF Aerospace, Asco, Avcorp, and extra producing tens of millions of holes.
"In aerospace manufacturing, it’s widespread to see longer-length drills," mentioned Cormier. "Whether it’s a 6-in.- or 12-in.-long drill, the fluting half is barely at the entrance because they’re only drilling via somewhat materials, however have to reach into locations to drill. We also see drills with adaptive shanks, which allow the drill to achieve across the nook to drill the opening, like within the facet beam of a fuselage. This style of drill drills at a 90-diploma angle; the operator is holding it straight but it’s drilling on the aspect with a threaded shank that’s on the HSS drill, which truly makes the outlet."
It actually depends on a shop’s holemaking frequency and overall manufacturing technique. A small or medium-measurement job shop that produces only one half that has eight holes in it may not need to spend a significant amount of cash on a drill. It might probably select the HSS choice, and although it could produce holes slower, the general cost per gap is also diminished.
"Plenty of job retailers, despite the fact that they might have a machine that runs coolant-by way of, will have a tendency to make use of HSS drills because of the price," stated Cormier. "They’re not making one million of something in order that they don’t want to worry about the run time in the identical means as someone like Linamar, where they are making thousands and thousands of holes. They might opt for a strong-carbide drill because, for them, savings of seconds per gap can equate to weeks’ value of production savings on a single shift."
Improving Productivity
One in all the major improvements in HSS drills has come from an evolving design. In keeping with Garud, a wider flute design permits for higher chip evacuation and helps with flood (external) coolant in addition to pecking.
Cormier added that one other enchancment was reinforcing the middle net of a HSS drill, significantly when it came to hand drilling operations.
Dormer’s A012 TiN tip drill resists flank and crater wear and has low friction, selling higher cutting speeds. Photo courtesy of Dormer Pramet.
"For the longest time that internet was consistently straight, that means the gullets had been constant the entire manner again on the drill," he explained. "We made the gullets less deep as you work your means again to the shank after which that centre internet tapered bigger, making the drill extra robust to withstand the rigors of all the hand drilling."
The consultants agreed that including enrichments and coatings is another way to enhance the drilling process. For instance, including an oxide therapy will enable the HSS to withstand heat better, allowing the drill to be used at faster RPMs.
"Cobalt enrichment improves the drill productivity," mentioned Garud. "Typically, 5 to eight per cent enrichment adds power and put on resistance. Vanadium provides heat resistance, offering some ability to run at barely greater speeds."
These different alloying components could be made through powdered metallurgy. Beyond this, the addition of tip coatings similar to TiAlN, TiCN, and CrN can improve heat resistance and the flexibility to run at quicker speeds.
Based on Dimitroff, these strategies add value however are aimed toward prolonging instrument life.
"Coatings typically enhance a tool’s hardness and its lubricity," he mentioned. "Hardness permits for the instrument to resist wear. Lubricity allows for the software to maneuver by material whereas avoiding constructed-up edge, which is materials galling or sticking to the drill. It additionally lowers temperatures the instrument is uncovered to whereas cutting, further increasing tool life."
Associate Editor Lindsay Luminoso could be reached at lluminoso@canadianmetalworking.com.
Dormer Pramet, www.dormerpramet.com
OSG, www.osgtool.com
Walter USA, www.walter-tools.com
Lindsay Luminoso
Associate Editor
Canadian Metalworking / Canadian Fabricating & Welding
1154 Warden Avenue
Toronto, M1R 0A1 Canada
Email Lindsay Luminoso
See More by Lindsay Luminoso
Lindsay Luminoso, affiliate editor, contributes to both Canadian Metalworking and Canadian Fabricating & Welding. She worked as an associate editor/web editor, at Canadian Metalworking from 2014-2016 and was most just lately an associate editor at Design Engineering.
댓글 0
번호 | 제목 | 글쓴이 | 날짜 | 조회 수 |
---|---|---|---|---|
4 | André Bertel's Karate-Do: August 2021 | Amee76417991910625 | 2022.02.24 | 7 |
» | Holemaking With High-Speed Steel Drills | WayneAbdullah725541 | 2022.02.15 | 3 |
2 | Bosch Impact Tough Titanium Drill Bit Set - Pro Tool Reviews | AltonNicholson5657 | 2022.02.05 | 2 |
1 | Why Don’t You Take A Look Online? | NatashaChester6505 | 2022.02.02 | 4 |